Oil Analysis III Training
Expertise to design a holistic analysis program
Oil Analysis III (OA III) is designed to give managers and reliability professionals the right knowledge to develop and implement a strong oil analysis program. Students will explore the most advanced levels of diagnostics and predictive maintenance and learn the metrics for program implementation and evaluation. This course also comes with supplemental training materials.
OA III Course Overview
- Course Duration: 32 hours (over 4 days)
- Associated Certifications: MLA III
- Prerequisites: OA II (Who should attend?)
- Study Pack: Not yet available
- Course Flyer: Download (PDF)
$1,995
Per student*
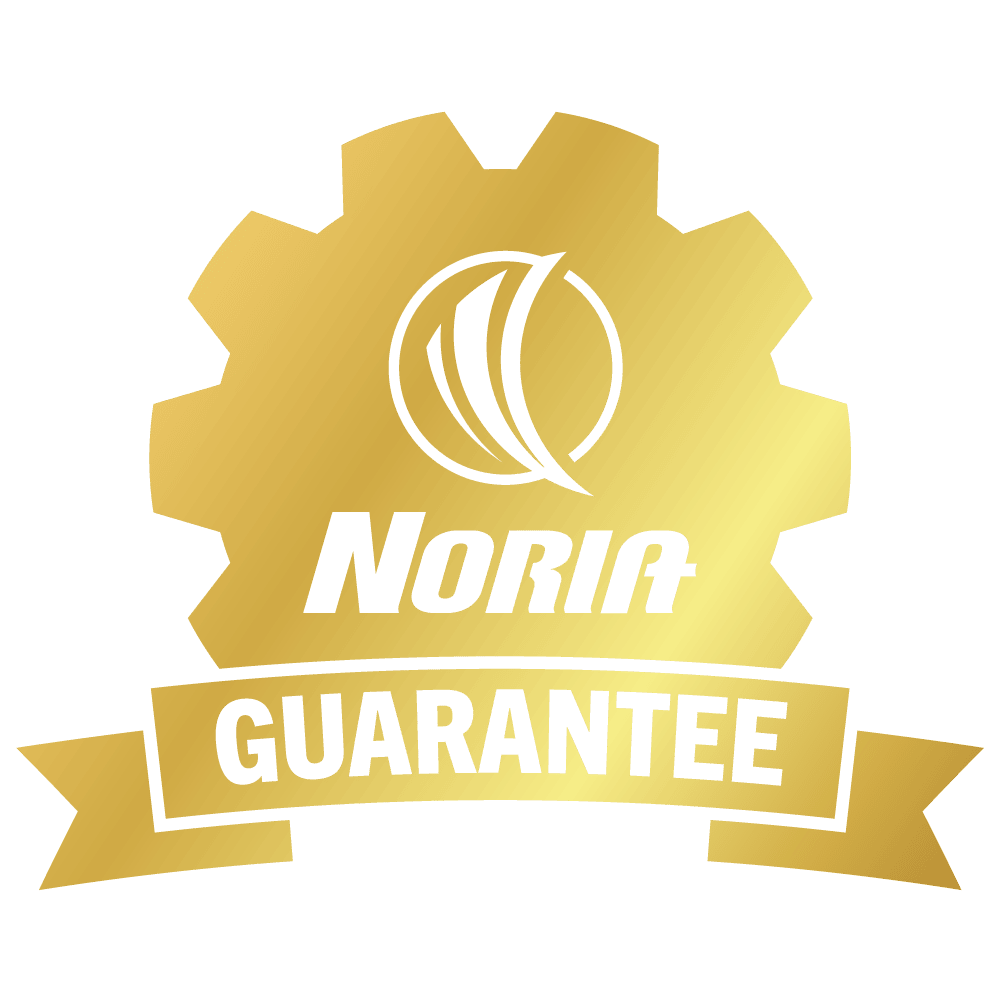

Upcoming Oil Analysis III training events
What you’ll learn
- Machine Wear
- Vibration and Oil Analysis
- Fluid Properties and Additive Depletion
- Contamination
- Analysis Technology
- Oil Analysis Program Design
Included with each course
One-year of Noria Academy access
You’ll get the ML I Study Pack including digital flash cards, a comprehensive practice exam to help you prepare for your certification exam, and over 5 hours of supplemental videos to help you build critical job skills. Access via our Noria Academy app or online at academy.noria.com.
Course Manual
Students who attend In-Person training or Live Online training in the United States will receive a printed copy of the course manual.
Recording of the course
If you purchased Live Online training, you can also opt to receive a recording of your course during registration for an additional fee. This recording will be accessible on-demand through our online Learning Management System for 90 days following completion of the course.
Getting Your MLA III Certification
Training with Noria can help you prepare for your certification exam, but all students who want to get certified need to apply in advance with the International Council for Machinery Lubrication (ICML) to take the exam. The ICML offers certification exams online and at all public Noria training events.
Our OA III course is aligned with the body of knowledge of the ICML’s MLA III certification.
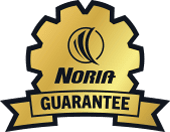
Noria Certification Guarantee
When you complete a Noria certification course, we guarantee you will pass the associated ICML exam — or get free resources and ongoing support from Noria experts until you do.
Learn from expert instructors
Gain valuable knowledge from these industry experts
-
Jim Fitch
-
Bennett Fitch
-
Wes Cash
-
Bob Scott
Senior Technical Consultant
Who should attend?
The Oil Analysis III course is most beneficial for maintenance, reliability and operations professionals who are directly responsible for lubrication tasks. Planners, supervisors and managers and others can also gain valuable insights into lubrication program gaps, cost-saving opportunities and data-driven decision-making from this course.
Job Title or Role |
Top Benefit |
---|---|
Lube Tech (Lubrication Technician) | Learn best practices for daily tasks |
Inspector | Uncover more actionable insights |
PdM Technician, Reliability Engineer, Maintenance Engineer | Improve data-driven decision-making |
Reliability Manager, Maintenance Manager | Identify program gaps and opportunities |
Course content
Noria’s most advanced analysis course, Oil Analysis III (OA III), teaches you high-level diagnostic, analysis and program design techniques. OA III is aligned with the body of knowledge of the International Council for Machinery Lubrication’s MLA III certification.
Day 1 | |
---|---|
Time | Section |
Morning | Introductions |
Lubrication Fundamentals | |
Lunch Break | |
Afternoon | Base Oil Fundamentals |
Understanding and Analyzing Machine Wear |
Day 2 | |
---|---|
Time | Section |
Morning | Understanding and Analyzing Machine Wear |
Lunch Break | |
Afternoon | Fluid Properties Analysis |
Additive Depletion |
Day 3 | |
---|---|
Time | Section |
Morning | Contamination, Filtration, Analysis |
Soot and Fuel Contamination | |
Corrosion Control | |
Lunch Break | |
Afternoon | Water affinity, Demulsibility, and Hydrolysis |
Onsite Oil Analysis Option |
Day 4 | |
---|---|
Time | Section |
Morning | Designing an Oil and Oil Analysis Program |
Wear Rates and Data | |
Optimum Reference State and Overall Machine Criticality | |
Lunch Break | |
Afternoon | Cost Benefit Analysis |
Case Studies |
Course formats
-
Public Events
Available In-Person or Live Online Worldwide
$1,995
Per student
Get in-person training with Noria experts and your ICML certification exam after the course (exam application required).
Calendar -
Private Live Online
Private, Virtual Classroom
$15,995
Per course
Join Noria experts LIVE in our virtual classroom—no hotel or travel costs required. Pricing includes up to 25 color manuals.
Learn More -
Studio Recordings
Available 24/7
$1,995
Per student
Get access to recordings of Noria training to learn on your own schedule.
Visit Noria Store -
On-site
At your facility
Starting at $16,825
Per course
Noria experts will come to your team, either in person at your plant or in a private live online classroom. Pricing includes up to 25 color manuals.
Learn More
Contact a Noria expert today
Frequently asked questions
What is check-in time for in-person training?
We ask that students check in on the first day of training (Tuesday) from 7:30 – 8:00 a.m.
How long does a day of training last?
A day of training typically begins at 8:00 a.m. and continues until 4:00 p.m. with an hour break for lunch.
Are food and beverages provided at in-person training events?
Complimentary fresh-brewed coffee will be available throughout the day, but students are responsible for their own food and drinks otherwise.
Is audio or video recording allowed during training?
No, please do not record audio or video of training course content.
Is parking included with registration for in-person training events?
No, parking fees are not included.
Other courses you may be interested in
-
Machinery Lubrication II
Machinery Lubrication II (ML II) covers advanced lubrication topics like lubricant selection, troubleshooting, predictive maintenance and more.
-
Oil Analysis II
Learn oil sampling best practices, how to identify improper additives or depletion, common contaminants, wear particles/faults and more.
-
Machinery Lubrication Engineer
Go beyond the traditional lubricant and lubrication subjects and undertake a holistic approach toward developing, implementing and managing a world-class lubrication program.