Lubricants contain a wealth of information
about the health of our machines
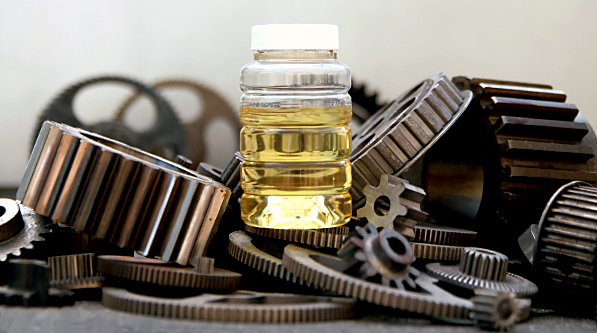
When failure occurs, finding the root of the problem can save time, money and headaches down the road. If you’re stumped by a recent or chronic failure problem, it might be time to call an expert.
Noria’s technical consulting team can come onsite to help you conduct inspections and perform detailed Root Cause Analysis (RCA) of components such as rolling-element bearings, gears, engines, pumps and others.
Our experience
We have led hundreds of failure investigations in almost every industry and specialized application
Industries we’ve served
-
Power generation
-
Pulp and paper
-
Mining and earthmoving
-
Marine and propulsion
-
Aerospace and defense
-
Oil and gas production
-
Food and beverage
-
Automotive and transport
-
and many more industries
We’ve performed failure investigations even in highly specialized applications
-
Shuttle program
-
Surgical drill bearings
-
U.S. Marine Corps
-
Titan missile program
Our failure analysis process
Noria failure analysis projects follow a sequence of steps that may vary somewhat depending on the nature of the failure, complexity, and associated machine type(s). Each is led by an experienced principal investigator (PI).
-
Assignment
Noria assigns one of our technical experts as your principal investigator (PI) for the case based on its type and complexity.
-
Submission
You submit a case file with any available background information (photos, operating data, failure history, timeline, troubleshooting studies, expert reports, lab work, drawings, etc.).
-
Study
Your PI studies the case file and makes a site visit for inspections, interviews, sampling, and to discuss potential root causes.
-
Testing
Samples go to the laboratory for testing. Your PI will work with you in advance to establish a testing budget that fits your goals.
-
Analysis
Your PI analyzes and interprets the lab data, delivering initial findings to you via conference call.
-
Delivery
Your PI delivers your final report and remediation plan, scheduling another call to discuss any further details.
Failure analysis services
-
Root cause analysis (RCA)
-
Tribological studies
-
Lubricant analysis (oil and grease)
-
Filter debris analysis
-
Ferrography and wear particle identification
-
Accelerated life testing
-
Metallography
-
Other related services available
Hundreds of success stories
Read about the problems and solutions to some of our
major failure analysis cases
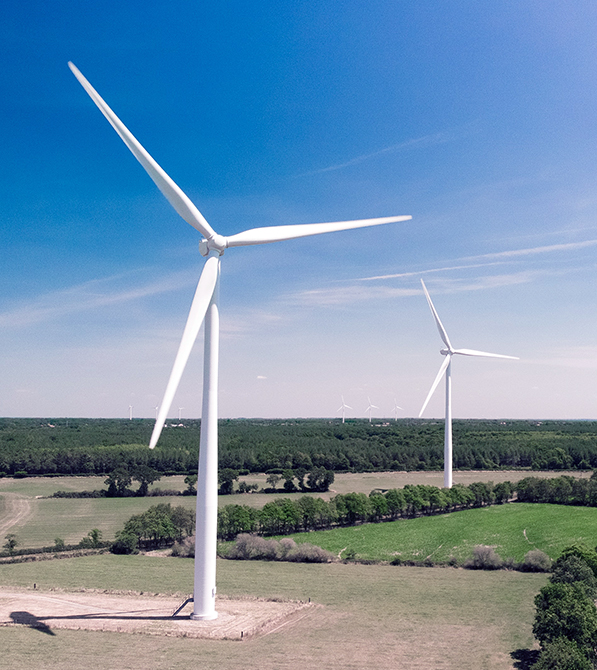
Rash of high temperature excursions in wind turbines
The problem
Wind energy utility contacted Noria after bearings in 100 wind turbine units triggered 1000+ high temperature alarms in a few months. Bearings were greased by an autoluber every day, but inspections showed significant operating wear that would soon lead to bearing failure in multiple units.
Other symptoms included:
- Grease catch pans collecting oil only (no grease) from bearings
- Thick or hardened grease observed on discharge side of bearings
- Grease from bearing cover had low oil content when analyzed
- Bearings had fresh grease in race area but also hardened grease
Failure analysis
Noria did a complete analysis of failed bearings, gathering data through lubricant analysis, metallography, ferrography and precursor condition monitoring to find the solution.
Perpetual turbine oil foam and air entrainment
The problem
A new combined-cycle power plant was having chronic foam problems with turbine oils in all three units:
- Lubricant supplier found nothing wrong with the lubricant supplied (it was new)
- OEM found nothing wrong with the oil or their units
- Oil analysis lab gave the new oil and in-service oil a clean bill-of-health
Failure analysis
Noria analyzed new and in-service lubricants as well as condition monitoring data. We examined lubricant handling hardware and interviewed maintenance personnel to help track down the source of the foam.
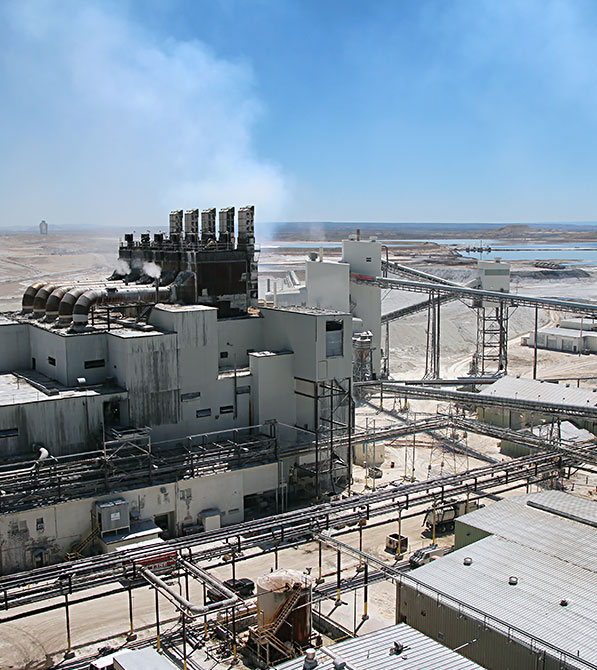
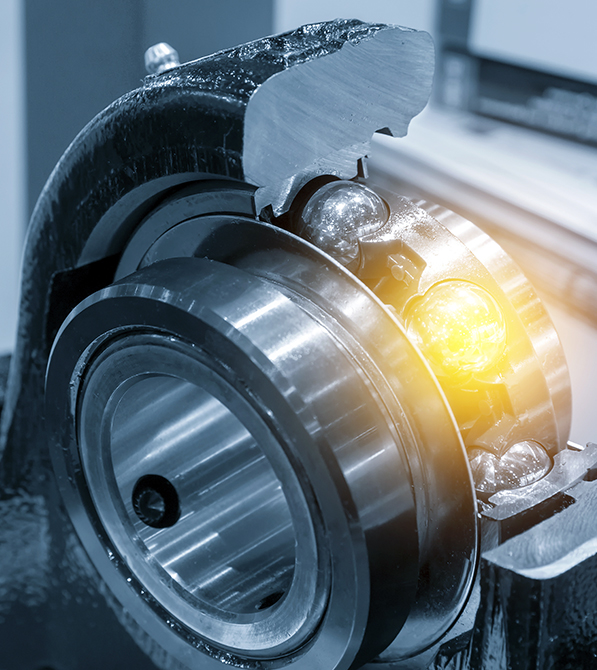
Chronic generator bearing failures
The problem
Owners of generator units were experiencing catastrophic bearing failures with a Mean Time Between Failures of 2,000 – 5,000 hours with these conditions observed:
- Deep groove, 52100 steel ball bearing—grease lubricated and hermetically sealed in a nitrogen gas environment
- Operating RPM of 1540 with unusual bearing spalls
- Inconsistencies with conventional failure modes
Failure analysis
Noria looked for evidence of potential causes like smearing, corrosion, electric current (pitting, fluting), fretting, clearance/fit problems, contamination, misalignment, and several other potential issues to find the cause of these bearing failures.
Contact a Noria expert today
Frequently asked questions
What laboratories are used?
Laboratories are selected for each case based on the nature of the failure, lubricant type and required test protocol. Because of the hundreds of commercial contract laboratories offering services, a discriminating approach to selection can be made for the benefit of the client in achieving efficient and accurate case outcome.
What other services/tests are offered?
Here is a selection of other services and tests that Noria experts can perform or interpret. If you are looking for something not listed here, contact us and we will likely be able to fulfill your need.
- Metallography and metallurgy
- Grease analysis
- Filter debris analysis
- Wear particle identification and characterization
- Particle contamination characterization
- Infrared and molecular spectroscopy
- Elemental spectroscopy (ICP, RDE, XRF, SEM-EDS, acid dissolution, etc.)
- Gas chromatography/mass spectrometry
- Radiological fluid testing
- Chemical microscopy
- ASTM lubricant performance testing
- In-service oil analysis
- Tribometry and film-strength testing
- Microbial contamination testing
- Aviation and aerospace fluid analysis
- Fire-resistant fluids analysis
- Varnish and sludge analysis