Lubrication Program Development
A well-designed lube program yields measurable results. Does yours?
Take the FREE Self-Assessment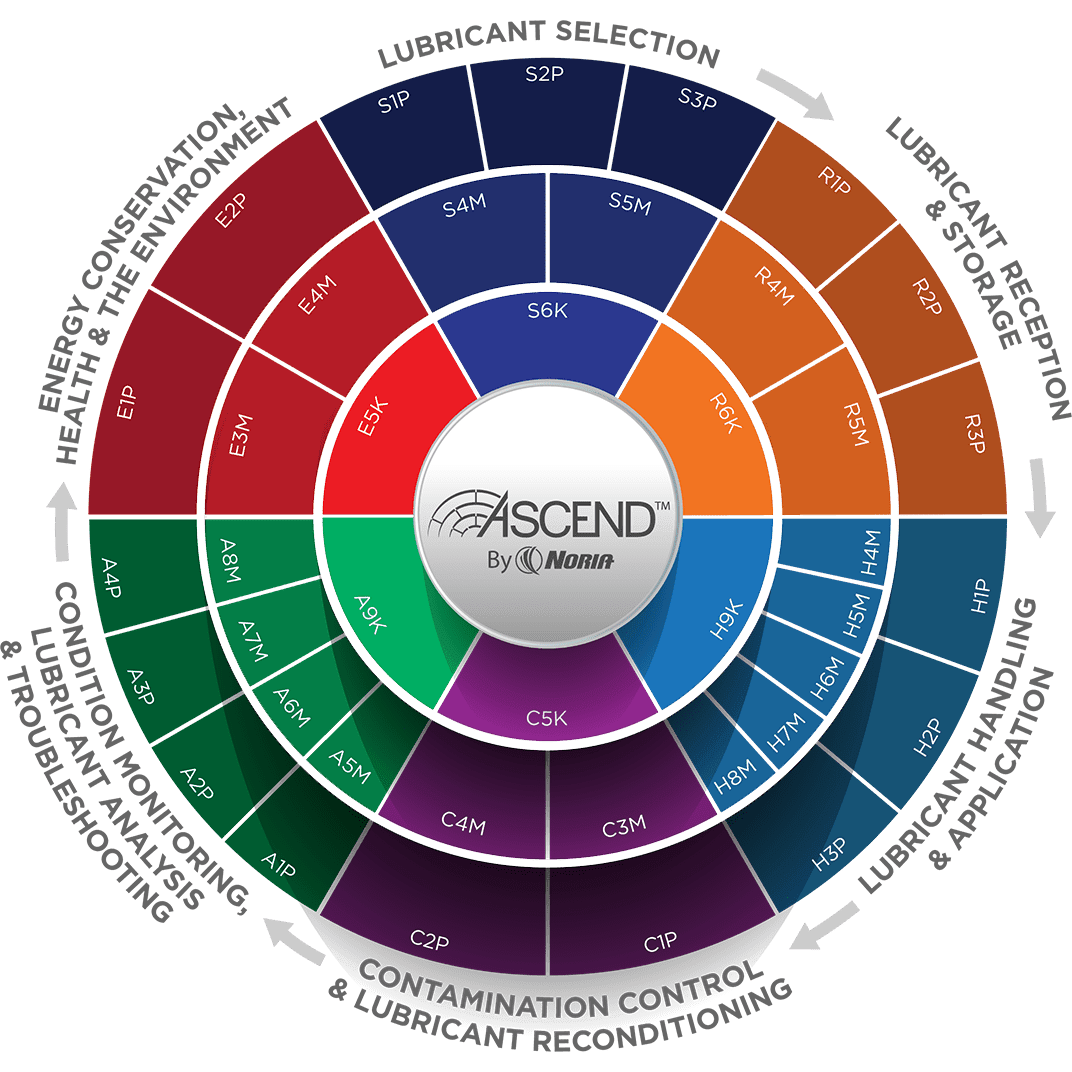
Prevent Mechanical Failure
Train personnel & maximize efficiency… All in one comprehensive program
Your lubrication program can be a profit-generator instead of a cost-center!
Let us show you how…
Lubricants are the lifeblood of machines. They are critical for keeping assets healthy and productive. And much like a blood test, analyzing lubricants can alert us to potentially life-threatening problems before it’s too late.
If improving reliability or lowering maintenance costs is your goal, it pays to look at your lubricants and lubrication practices carefully and holistically. Are lubrication staff properly trained? Are lubricants kept clean enough? Are oil change or regrease intervals set properly? Are recent machine failures related to lubrication?
Answering these questions (and more) is the beginning of Lubrication Program Development (LPD). Noria experts use this holistic, three-phase process to help customers identify gaps in their lubrication programs and make a prioritized plan for improvements.
Build a reliable lubrication program
- Reduce downtime
- Promote reliability culture
- Minimize costs
- Establish KPIs to measure progress
- Streamline for efficiency
- Deliver significant ROI
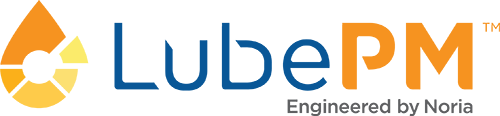
Your 3-phase plan to a better bottom line
-
Ascend Assessment
Get a customized roadmap for quick wins and long-term success, along with training, KPIs, and a detailed report to help you cost-justify improvements.
Help me get started -
Engineering Design
Noria experts survey your lubricated assets, collecting all the data needed to deliver comprehensive procedures along with lubricant and hardware recommendations.
Learn more -
Program Implementation
Noria facilitates the vendor selection and procurement process to outfit your program with equipment and hardware you need to achieve your reliability and maintenance goals.
Learn more
Success Stories
Case studies from our customers
Learn how you can drive success with lubrication
Lubrication & Contamination Done Right from the Start
at Blue Buffalo
When Blue Buffalo called Noria, they were in the process of designing and building their 450,000-square-foot Richmond plant. Before machines were installed, they worked with Noria to ensure that the right inspections, contamination control activities and lubrication procedures would be in place from day one. Over the course of a year, Noria visited the plant six times to identify lubrication points, document procedures and train staff. The plant was subsequently the recipient of the 2021 John R. Battle Award for lubrication excellence, showcasing its dedication to best practices and continuous improvement.
Lubrication program enables Simmons Feed to cut downtime by 50%
The Simmons Feed Ingredients plant in Southwest City, Missouri, brought in Noria consultants to develop a road map for lubrication excellence. After implementing Noria’s Lubrication Program Development and training, the facility was able to achieve cleaner oil, prevent machine failures, avoid lost production and save up to $1 million a year.
Hardware creates culture change at Argos Newberry
The Argos Cement Plant in Newberry, Florida, had a directive from their corporate team to improve lubrication procedures and hardware but needed help getting started. After receiving Noria training and an Ascend Assessment, the plant was able to work with the Noria team to identify better lubricant handling options, more effective greasing techniques and opportunities for better contaminant exclusion and removal. Their success has encouraged the Argos team to implement similar improvements in their other plants as well.
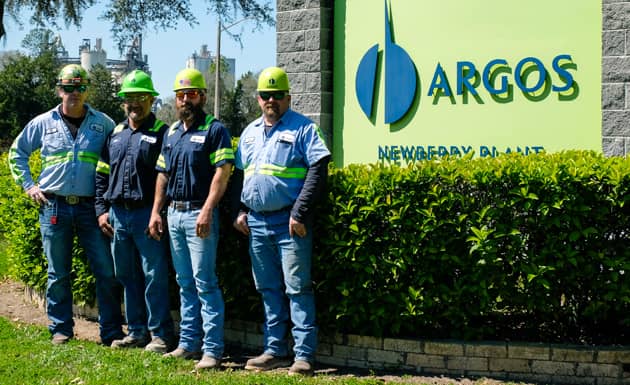
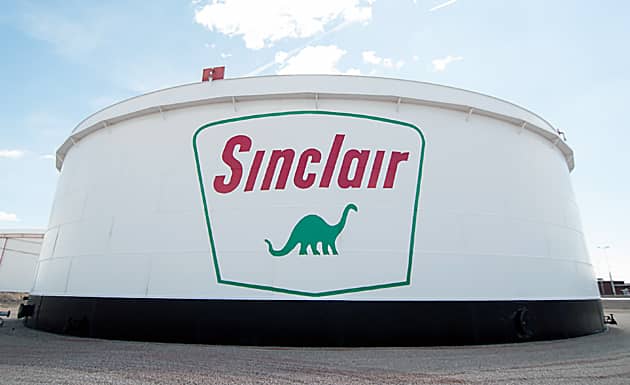
Proactive maintenance approach at Sinclair impacts bottom line
Noria’s onsite training and Lubrication Program Development helped transform the Sinclair Wyoming Refinery into an industry leader for machinery lubrication. With guidance from Noria, the refinery was able to shift to a proactive maintenance approach and adopt best practices, significantly impacting its operations and bottom line.
Contact a Noria expert today
Frequently asked questions
Who can benefit from LPD?
Anyone who makes decisions about lubrication in their worksite, plant or facility can lead a lubrication program development effort. Noria experts will be with you every step of the way to answer questions and provide recommendations for success.
How long is the process?
Lubrication Program Development (LPD) is divided into three phases, each one is listed with its average timeline below:
Phase I: Ascend Assessment
1 week
Phase II: Engineering Design
6 – 8 weeks
Phase III: Implementation
1 – 2 years